Rim Clamp solves pipe ovality issues
The oil and gas pipeline industry has had a challenging few years as a result of the global economic conditions and the low oil price. Contractors are increasingly looking for ways to reduce costs when budgeting for projects, and increasingly this has led to an increase in pipes being supplied from emerging markets. This, when coupled with the move to higher strength steel for pipe with thinner wall thickness, in order to minimize freight costs, steel costs, and filler metal costs, has seen many contractors noticing a significant increase in new pipes arriving with out of round issues.
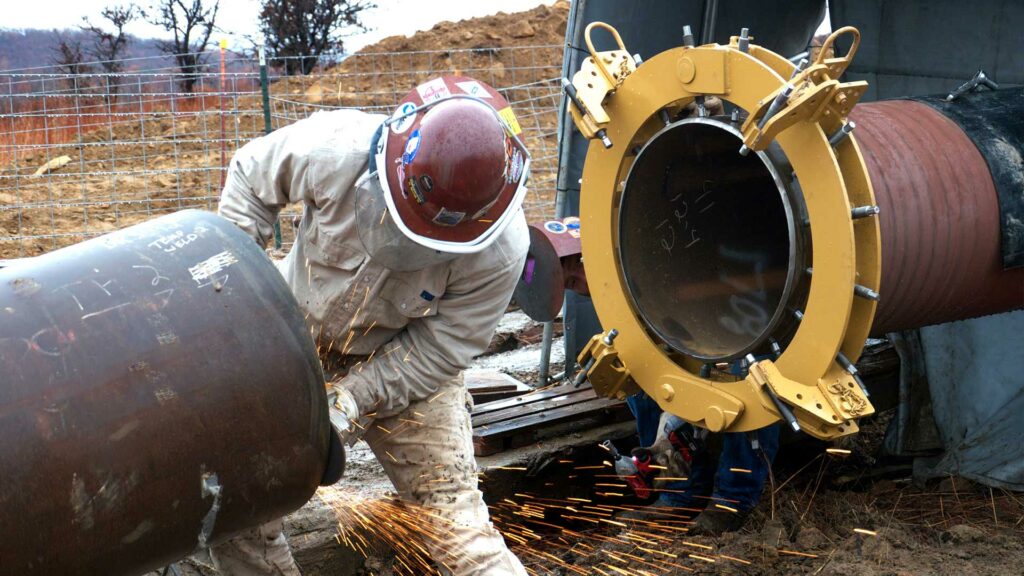
When welding pipes on a right of way, accuracy is key. Even the slightest misalignment can result in a weld failing inspection, and cut outs are a cost every contractor is keen to avoid. Weld process naturally plays a key part in this, and SMAW and GMAW welders are acutely aware of the differing requirements between thinner and thicker walled pipes, and the issues caused by hydrogen cooling more quickly and taking longer to diffuse to the surface due to increased distance. Despite this, when coaxial alignment of pipes is not possible due to out of round conditions being so far out of tolerance, no amount of welder skill or weld process adherence can fix the issue.
For automated welding, coaxial alignment becomes even more of a concern. Recent years have seen a large increase in the amount of cross country pipelines utilizing automatic welding systems due to their low labor intensity, high weld speed, uniform weld quality and precision finishes. Pipes which are slightly out of round, however, will result in considerably more filler metals being required on a weld, and pipe which are moderately to heavily out of round will often result in a weld defect that fails inspection. Where a manual pipe welder would likely notice a misalignment, even if it was missed by a pipefitter; an automated system will not, and will continue as programmed. Thus the risk of a cut out being required becomes even greater.
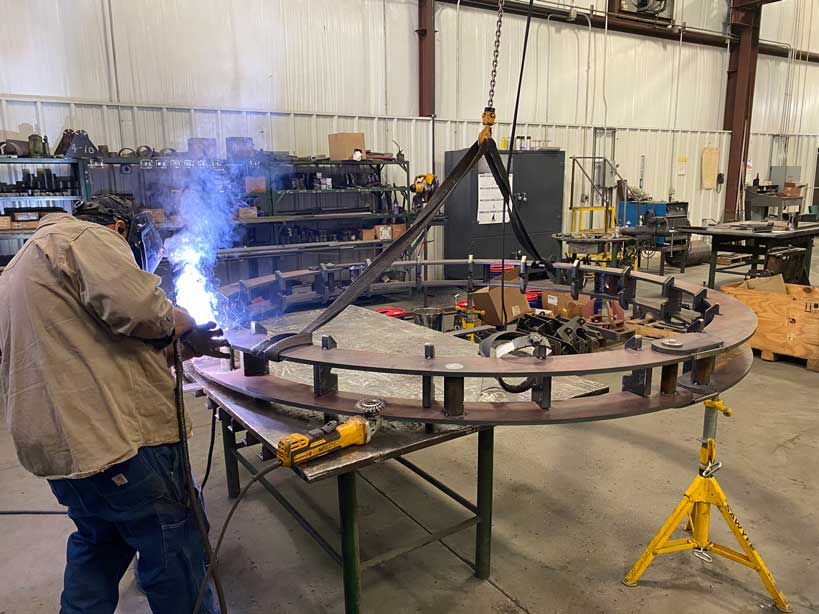
Sawyer Manufacturing Company in Tulsa, OK, USA have invested a significant amount of time talking to pipe welders both across the US and internationally about the issues they face in day to day welding operations. Out of round pipes causing root gap misalignment and the huge amount of lost man hours to correcting the issue is one concern which is mentioned time and time again; exasperating pipefitters across the world.
The majority of cross country pipelines use pneumatically powered internal line up clamps to set up and maintain a root gap for a welder or automated welder to put in the root pass or tack weld, depending on the process being used. These clamps are powerful units, designed to exert internal pressure onto the pipes in order to create the required coaxial alignment, whilst not damaging the interior of the pipe. For out of round conditions, however, these units are not capable of reforming pipes to bring them back into round, and therefore alternative methods must be sought.
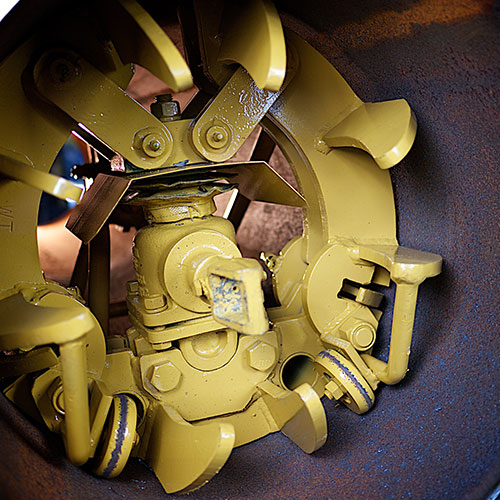
Similarly, not all conditions are suitable for these type of internal clamps. When dealing with elbows, reducers, lobsterback weld sections, or any significant curved sections of the pipe, external clamping solutions are required.
Of course there are many other pipeline situations other than installing new pipe to new pipe on a cross country pipeline. Out of round is even more prevalent on old pipes which have been subject to adverse weather conditions over time, or buried underground for significant periods. Again, when segments are due for replacement, or a cut out is required due to a leak or pipe deterioration; out of round becomes a significant issue when pipefitters come to install a replacement piece of new pipe to the existing weather beaten pipe.
As a manufacturer of both internal and external clamping solutions for pipefitters and welders, it is not unusual for clients to approach Sawyer with out of round conditions of 2” on their pipeline; and asking for a solution to the issue. The days of low wall thickness and low yield steel pipes are long behind us as an industry, and as such reforming a pipe back into round requires considerably more exertion of force, and precision, than it did in the days of our grandfathers. Whilst “beatin’ it into submission’ may have been the reforming method in days gone by, when faced with a 72” X70 pipe with a 1” wall thickness, even Thor’s hammer is unlikely to provide you with an adequate tool. Plus modern day Quality Control processed are unlikely to allow it.
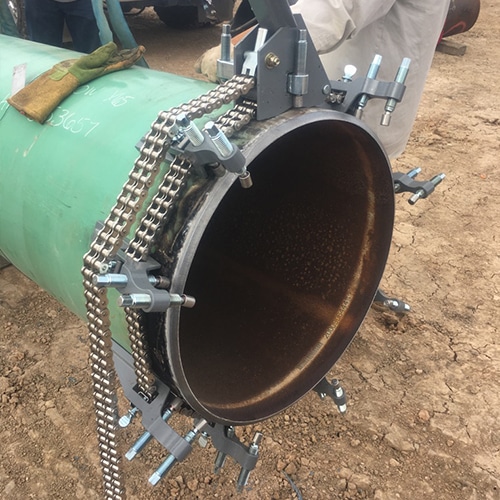
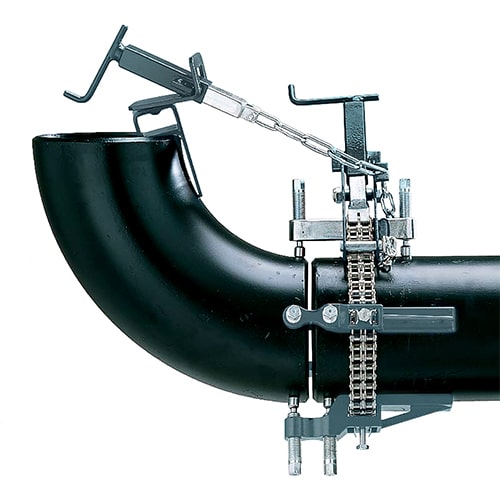
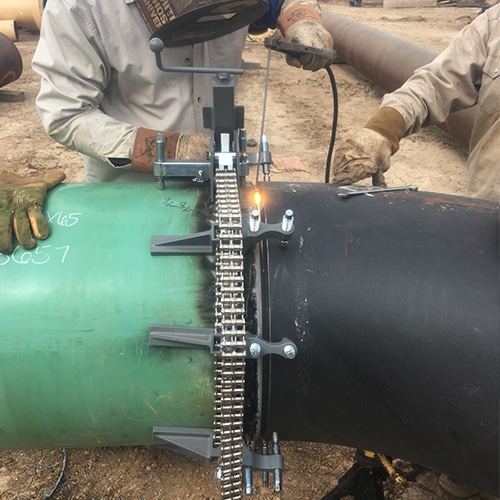
For modern pipeline applications, surprisingly it is an older design of tool which is still used for reforming smaller pipes with lower levels of ovality; though the design is much changed from its original form. The Chain Clamp is a powerful and versatile ally for pipe fitters using SMAW or GMAW welding processes, or for welders who manually tack pipes into place before setting up an automatic welding machine. Arched jackbars and thick reforming screws provide the necessary reforming pressure on out of round pipe, and the arched jackbars allow for full circle access to the pipe for manual welding processes.
These clamps have been used for generations, in one configuration or another, due to their versatility for use on elbows, tees, flanges, reducers, etc. and of course for their ability to solve light to moderate out of round issues on a pipeline.
Modern pipes, however, have recently presented the industry with such ovality issues that the Schedule 40 reforming capability of the Chain Clamps is exceeded. Thus, manufacturers of pipeline equipment have had to come up with new solutions for solving this issue for pipefitters and welders; and for a time that solution came in the form of a Double Chain Clamp. This product offers twice the reforming capability of a standard Chain Clamp, with its twin chains and increased size jackbars and reforming screws.
These options are known by pipe fitters across the world. It is one of the few pipeline fit up products manufactured by Sawyer which are sold in every international market in which they deal. The Chain Clamps have been a staple of the pipeline fit up industry for decades, and will almost certainly continue to be utilized for generations of pipefitters to come.

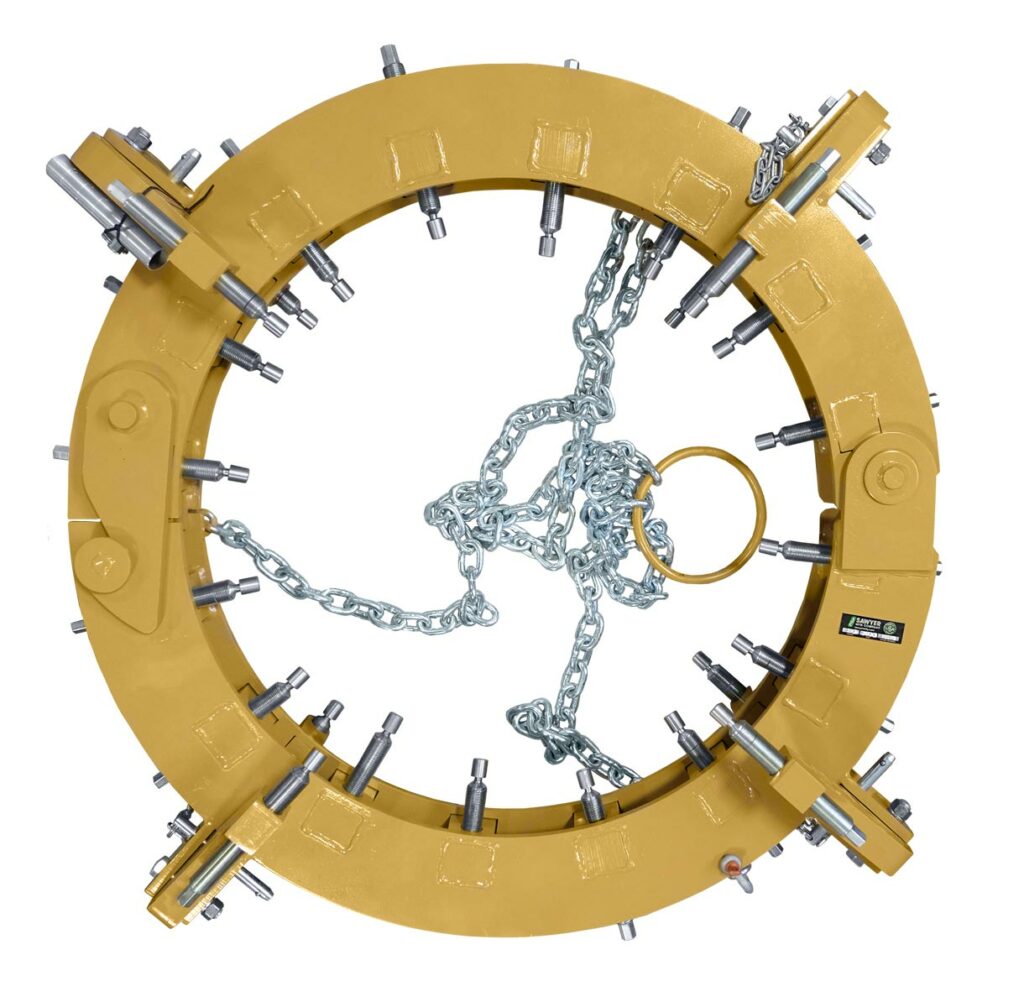
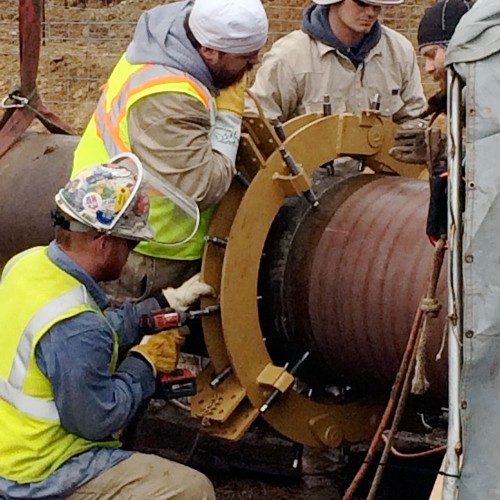
Unfortunately modern applications are creating the issue is that pipefitters are increasingly being presented with out of round conditions which are out of the scope even of the Double Chain Clamps. The 72” X70 1” wall thickness pipe mentioned earlier, with 1” out of round conditions, would be an example of such a challenge; yet 2016 saw Sawyer presented with even bigger challenges. Smaller diameter pipes are increasingly being discovered to have significantly exacting ovality issues, and even Schedule 80 reforming capabilities are not enough to subjugate these kind of pipes.
It is for applications such as these that pipefitters are increasingly turning to Sawyer’s heavy duty RIM Clamps, which offer huge reforming capability due to their robust outer frames and powerful reforming screws. The additional benefit of these clamps over their Chain Clamp cousins is that the hinged jackbars allow for 100% access to the weld gap for welding and grinding, without the release of welding pressure.
Manufactured from A36 steel, and coupled with 1 1/16” reforming screws, the Sawyer Ultra RIM Clamp has been completely redesigned in the past 12 months to provide the ultimate in reforming capability to deal with these ever-increasing ovality issues on higher yield steels; even when clad with titanium.
It is these clamps which are providing the necessary correction of ovality in pipelines across the world; allowing pipefitters and welders to achieve the necessary coaxial alignment of pipes on the right of way. It’s not quite Thor’s hammer, but the Sawyer RIM Clamp is proving to be a valuable tool when it comes to conquering these heavy duty out of round conditions.
Follow us on Facebook and Instagram to see what we are doing and our equipment in use.
Watch our product videos on our YouTube channel.